Il microscopio elettronico a scansione è stato utilizzato per osservare la frattura per fatica e analizzare il meccanismo di frattura; allo stesso tempo, è stata effettuata una prova di fatica da centrifugazione sui provini decarburati a diverse temperature per confrontare la durata a fatica dell'acciaio di prova con e senza decarburazione e per analizzare l'effetto della decarburazione sulle prestazioni a fatica dell'acciaio di prova. I risultati mostrano che, a causa della contemporanea esistenza di ossidazione e decarburazione nel processo di riscaldamento, l'interazione tra le due, determinando lo spessore dello strato completamente decarburato con l'aumento della temperatura mostra un andamento crescente e poi decrescente, la lo spessore dello strato completamente decarburato raggiunge un valore massimo di 120 μm a 750 ℃, e lo spessore dello strato completamente decarburato raggiunge un valore minimo di 20 μm a 850 ℃, e il limite di fatica dell'acciaio di prova è di circa 760 MPa, e la fonte delle cricche da fatica nell'acciaio di prova sono principalmente le inclusioni non metalliche di Al2O3; il comportamento di decarburazione riduce notevolmente la durata a fatica dell'acciaio di prova, influenzando le prestazioni a fatica dell'acciaio di prova, più spesso è lo strato di decarburazione, minore è la durata a fatica. Al fine di ridurre l'impatto dello strato di decarburazione sulle prestazioni a fatica dell'acciaio di prova, la temperatura ottimale del trattamento termico dell'acciaio di prova dovrebbe essere impostata a 850℃.
L'ingranaggio è una componente importante dell'automobile, a causa del funzionamento ad alta velocità, la parte ingranante della superficie dell'ingranaggio deve avere elevata robustezza e resistenza all'abrasione, e la radice del dente deve avere buone prestazioni di fatica a flessione a causa del carico ripetuto e costante, al fine di evitare crepe che portano al materiale frattura. La ricerca mostra che la decarburazione è un fattore importante che influenza le prestazioni di fatica da centrifugazione dei materiali metallici e le prestazioni di fatica da centrifugazione sono un indicatore importante della qualità del prodotto, quindi è necessario studiare il comportamento di decarburazione e le prestazioni di fatica da centrifugazione del materiale di prova.
In questo articolo, il forno per il trattamento termico del test di decarburazione della superficie dell'acciaio per ingranaggi 20CrMnTi analizza diverse temperature di riscaldamento sulla profondità dello strato di decarburazione dell'acciaio di prova della legge mutevole; utilizzando la macchina per prove di fatica a trave semplice QBWP-6000J sulla prova di fatica a flessione rotante dell'acciaio di prova, determinazione delle prestazioni di fatica dell'acciaio di prova e allo stesso tempo per analizzare l'impatto della decarburazione sulle prestazioni di fatica dell'acciaio di prova per migliorare la produzione effettiva il processo di produzione, migliorare la qualità dei prodotti e fornire un riferimento ragionevole. La prestazione a fatica dell'acciaio di prova è determinata dalla macchina per prove di fatica a flessione in rotazione.
1. Materiali e metodi di prova
Materiale di prova per un'unità che fornisce acciaio per ingranaggi 20CrMnTi, la composizione chimica principale come mostrato nella Tabella 1. Test di decarburazione: il materiale di prova viene trasformato in un campione cilindrico da Ф8 mm × 12 mm, la superficie deve essere brillante senza macchie. Il forno per il trattamento termico è stato riscaldato a 675 ℃, 700 ℃, 725 ℃, 750 ℃, 800 ℃, 850 ℃, 900 ℃, 950 ℃, 1.000 ℃, nel campione e mantenuto per 1 ora, quindi raffreddato ad aria a temperatura ambiente. Dopo il trattamento termico del campione mediante impostazione, molatura e lucidatura, con erosione della soluzione alcolica di acido nitrico al 4%, l'uso della microscopia metallurgica per osservare lo strato di decarburazione dell'acciaio di prova, misurando la profondità dello strato di decarburazione a diverse temperature. Prova di fatica da flessione in rotazione: il materiale di prova secondo i requisiti della lavorazione di due gruppi di campioni di fatica da flessione in rotazione, il primo gruppo non esegue il test di decarburazione, il secondo gruppo di test di decarburazione a temperature diverse. Utilizzando la macchina per prove di fatica a flessione in rotazione, i due gruppi di acciaio di prova per prove di fatica a flessione in rotazione, determinazione del limite di fatica dei due gruppi di acciaio di prova, confronto della durata a fatica dei due gruppi di acciaio di prova, uso della scansione osservazione della frattura per fatica al microscopio elettronico, analizzare le ragioni della frattura del campione, per esplorare l'effetto della decarburazione delle proprietà di fatica dell'acciaio di prova.
Tabella 1 Composizione chimica (frazione di massa) dell'acciaio di prova% in peso
Effetto della temperatura di riscaldamento sulla decarburazione
La morfologia dell'organizzazione della decarburazione a diverse temperature di riscaldamento è mostrata in Fig. 1. Come si può vedere dalla figura, quando la temperatura è di 675 ℃, sulla superficie del campione non appare uno strato di decarburazione; quando la temperatura sale a 700 ℃, inizia ad apparire lo strato di decarburazione superficiale del campione, per il sottile strato di decarburazione di ferrite; con l'aumento della temperatura fino a 725 ℃, lo spessore dello strato di decarburazione della superficie del campione è aumentato in modo significativo; Lo spessore dello strato di decarburazione a 750 ℃ raggiunge il suo valore massimo, in questo momento il grano di ferrite è più chiaro, grossolano; quando la temperatura sale a 800 ℃, lo spessore dello strato di decarburazione inizia a diminuire in modo significativo, il suo spessore scende alla metà dei 750 ℃; quando la temperatura continua a salire fino a 850 ℃ e lo spessore della decarburazione è mostrato in Fig. 1. 800 ℃, lo spessore dell'intero strato di decarburazione ha iniziato a diminuire in modo significativo, il suo spessore è sceso a 750 ℃ quando era dimezzato; quando la temperatura continua a salire fino a 850 ℃ e oltre, lo spessore dello strato di decarburazione completo dell'acciaio di prova continua a diminuire, lo spessore di metà strato di decarburazione inizia ad aumentare gradualmente fino a quando la morfologia dello strato di decarburazione completa scompare, la morfologia di metà strato di decarburazione gradualmente scompare. Si può notare che lo spessore dello strato completamente decarburato con l'aumento della temperatura è stato prima aumentato e poi ridotto, il motivo di questo fenomeno è dovuto al campione nel processo di riscaldamento contemporaneamente al comportamento di ossidazione e decarburazione, solo quando la velocità di decarburazione è più veloce della velocità di ossidazione e apparirà il fenomeno della decarburazione. All'inizio del riscaldamento, lo spessore dello strato completamente decarburato aumenta gradualmente con l'aumento della temperatura fino a quando lo spessore dello strato completamente decarburato raggiunge il valore massimo, in questo momento per continuare ad aumentare la temperatura, la velocità di ossidazione del campione è più veloce di il tasso di decarburazione, che inibisce l'aumento dello strato completamente decarburato, determinando una tendenza al ribasso. Si può vedere che, nell'intervallo 675 ~950 ℃, il valore dello spessore dello strato completamente decarburato a 750 ℃ è il più grande, e il valore dello spessore dello strato completamente decarburato a 850 ℃ è il più piccolo, pertanto, si consiglia che la temperatura di riscaldamento dell'acciaio di prova sia di 850 ℃.
Fig.1 Istomorfologia dello strato decarburato di acciaio di prova mantenuto a diverse temperature di riscaldamento per 1 ora
Rispetto allo strato semi-decarburato, lo spessore dello strato completamente decarburato ha un impatto negativo più grave sulle proprietà del materiale, ridurrà notevolmente le proprietà meccaniche del materiale, come la riduzione della resistenza, della durezza, della resistenza all'usura e del limite di fatica , ecc., e aumentano anche la sensibilità alle crepe, influenzando la qualità della saldatura e così via. Pertanto, il controllo dello spessore dello strato completamente decarburato è di grande importanza per migliorare le prestazioni del prodotto. La Figura 2 mostra la curva di variazione dello spessore dello strato completamente decarburato con la temperatura, che mostra più chiaramente la variazione dello spessore dello strato completamente decarburato. Dalla figura si può vedere che lo spessore dello strato completamente decarburato è solo di circa 34μm a 700°C; con l'aumento della temperatura a 725 ℃, lo spessore dello strato completamente decarburato aumenta significativamente fino a 86 μm, che è più di due volte lo spessore dello strato completamente decarburato a 700 ℃; quando la temperatura sale a 750 ℃, lo spessore dello strato completamente decarburato Quando la temperatura sale a 750 ℃, lo spessore dello strato completamente decarburato raggiunge il valore massimo di 120 μm; man mano che la temperatura continua a salire, lo spessore dello strato completamente decarburato inizia a diminuire bruscamente, fino a 70 μm a 800°C, e poi al valore minimo di circa 20μm a 850°C.
Fig.2 Spessore dello strato completamente decarburato a diverse temperature
Effetto della decarburazione sulle prestazioni a fatica nello spin bending
Al fine di studiare l'effetto della decarburazione sulle proprietà di fatica dell'acciaio per molle, sono stati condotti due gruppi di prove di fatica a flessione in rotazione, il primo gruppo era prove di fatica direttamente senza decarburazione, e il secondo gruppo era prove di fatica dopo decarburazione alla stessa sollecitazione. livello (810 MPa) e il processo di decarburazione è stato mantenuto a 700-850 ℃ per 1 ora. Il primo gruppo di campioni è mostrato nella Tabella 2, che rappresenta la vita a fatica dell'acciaio per molle.
La vita a fatica del primo gruppo di provini è mostrata nella Tabella 2. Come si può vedere dalla Tabella 2, senza decarburazione, l'acciaio di prova è stato sottoposto solo a 107 cicli a 810 MPa e non si è verificata alcuna frattura; quando il livello di stress ha superato gli 830 MPa, alcuni provini hanno cominciato a fratturarsi; quando il livello di sollecitazione superava gli 850 MPa, i provini di fatica erano tutti fratturati.
Tabella 2 Vita a fatica sotto diversi livelli di stress (senza decarburazione)
Per determinare il limite di fatica, viene utilizzato il metodo di gruppo per determinare il limite di fatica dell'acciaio di prova e, dopo l'analisi statistica dei dati, il limite di fatica dell'acciaio di prova è di circa 760 MPa; per caratterizzare la vita a fatica dell'acciaio di prova sotto diverse sollecitazioni, viene tracciata la curva SN, come mostrato in Figura 3. Come si può vedere dalla Figura 3, diversi livelli di sollecitazione corrispondono a diversa vita a fatica, quando la vita a fatica di 7 , corrispondente al numero di cicli per 107, il che significa che il provino in queste condizioni attraversa lo stato, il valore di sollecitazione corrispondente può essere approssimato come valore di resistenza alla fatica, ovvero 760 MPa. Si può vedere che la curva S - N è importante per la determinazione della vita a fatica del materiale e ha un importante valore di riferimento.
Figura 3 Curva SN del test sperimentale di fatica a flessione rotante dell'acciaio
La vita a fatica del secondo gruppo di provini è mostrata nella Tabella 3. Come si può vedere dalla Tabella 3, dopo che l'acciaio in prova è stato decarburato a diverse temperature, il numero di cicli è ovviamente ridotto, e sono più di 107, e tutti i provini di fatica sono fratturati e la durata a fatica è notevolmente ridotta. In combinazione con lo spessore dello strato decarburato di cui sopra con la curva di cambiamento della temperatura si può vedere, lo spessore dello strato decarburato di 750 ℃ è il più grande, corrispondente al valore più basso della durata a fatica. Lo spessore dello strato decarburato di 850 ℃ è il più piccolo, corrispondente al valore di durata a fatica relativamente alto. Si può vedere che il comportamento di decarburazione riduce notevolmente le prestazioni a fatica del materiale e quanto più spesso è lo strato decarburato, tanto minore è la durata a fatica.
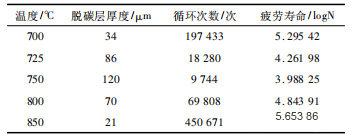
Tabella 3 Vita a fatica a diverse temperature di decarburazione (560 MPa)
La morfologia della frattura per fatica del campione è stata osservata al microscopio elettronico a scansione, come mostrato in Fig. 4. Figura 4(a) per l'area della fonte della cricca, nella figura si può vedere un evidente arco di fatica, secondo l'arco di fatica per trovare la fonte di fatica, si può vedere, la fonte di cricca per le inclusioni non metalliche "fish-eye", inclusioni che facilmente causano concentrazione di stress, con conseguente cricche da fatica; Fig. 4(b) per la morfologia dell'area di estensione della fessura, si possono vedere evidenti strisce di fatica, aveva una distribuzione simile a un fiume, appartiene a una frattura quasi dissociativa, con crepe che si espandono, portando infine alla frattura. La Figura 4(b) mostra la morfologia dell'area di espansione delle fessure, si possono vedere evidenti strisce di fatica, sotto forma di distribuzione simile a un fiume, che appartiene alla frattura quasi dissociativa, e con l'espansione continua delle fessure, che alla fine porta alla frattura .
Analisi della frattura a fatica
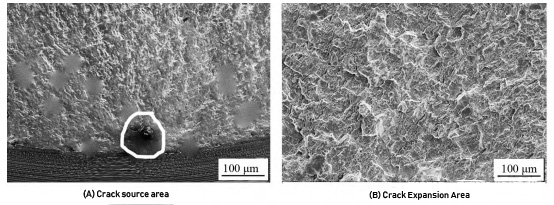
Fig.4 Morfologia SEM della superficie di frattura per fatica dell'acciaio sperimentale
Per determinare il tipo di inclusioni in Fig. 4, è stata effettuata l'analisi della composizione dello spettro energetico e i risultati sono mostrati in Fig. 5. Si può vedere che le inclusioni non metalliche sono principalmente inclusioni di Al2O3, indicando che le inclusioni sono la principale fonte di cricche causate dalla rottura delle inclusioni.
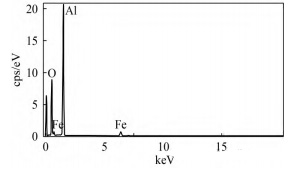
Figura 5 Spettroscopia energetica delle inclusioni non metalliche
Concludere
(1) Posizionando la temperatura di riscaldamento a 850 ℃ si ridurrà al minimo lo spessore dello strato decarburato per ridurre l'effetto sulle prestazioni a fatica.
(2) Il limite di fatica della prova di flessione in rotazione dell'acciaio è 760 MPa.
(3) L'acciaio di prova si fessura in inclusioni non metalliche, principalmente miscele di Al2O3.
(4) la decarburazione riduce seriamente la durata a fatica dell'acciaio di prova, più spesso è lo strato di decarburazione, minore è la durata a fatica.
Orario di pubblicazione: 21 giugno 2024